High Performance Engineering Plastics for the Food Processing Industry
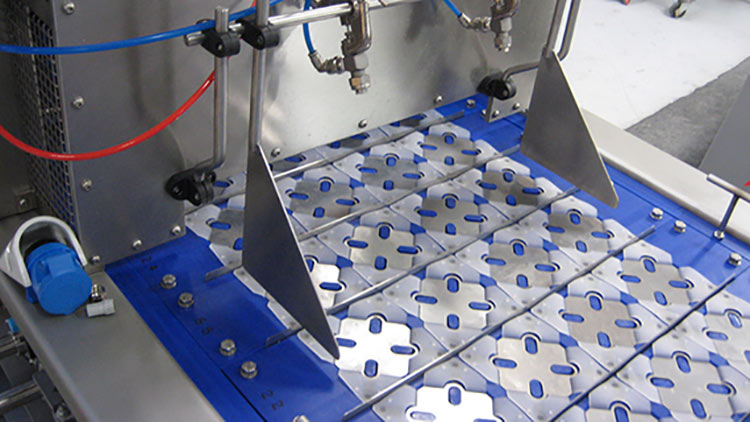
One of the largest distributors and fabricators of engineering plastics in the United States, Modern Plastics provides FDA approved polymers to the food processing industry.
We have compiled this list to inform you of the various ultra-detectable, food safe plastics we use to serve the food processing industry.
To help avoid recalls and contaminations, many food grade plastics are made with special X-Ray and metal detectable materials as well as being blue per food processing industry standards for easier visual detectability.
Modern Plastics provides food grade materials that are heat resistant, chemical resistant, and high wear resistant making these plastics versatile for food grade applications.
If you have a question about any of the plastics mentioned, our experts will be happy to assist you – contact us here or tap Interested in Our Services to email or text us at any time.
Why Trust Modern Plastics?
Modern Plastics has led by setting new industry standards throughout its 75 years in plastics distribution.
Modern Plastics is an ISO-Certified company (9001:2015 and AS9120B, 9001:2015 and AS9100D & 13485:2016) with a large inventory compliant to USA FDA Compliance, Federal Regulation (21 CFR) or FDA FCN, USDA, NSF 51 and NSF 61, and 3-A Dairy Compliant Plastics specifications.
Our knowledgeable Sales & Quality staff have over 25 years of experience servicing the food processing industry.
We inventory high performance plastics that are lot controlled, individually line marked and bar-coded for complete material traceability.
Learn more about our services here.
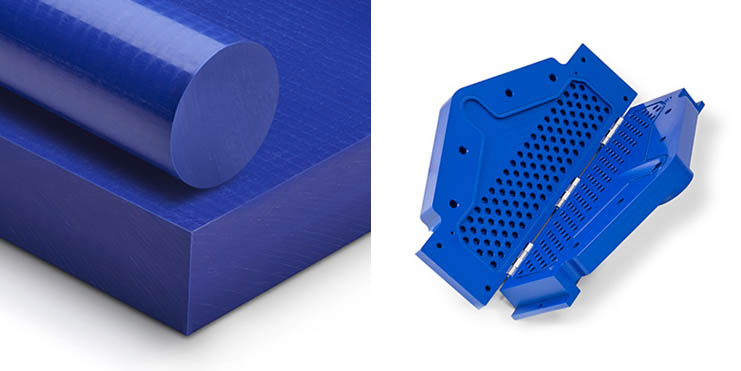
Acetal (Delrin®) Food Processing Plastics
Food Grade Acetal and Delrin®
Below is a list highlighting specific Food Grade Acetal (Delrin®) we supply:
- Ensinger TECAFORM® AH FG Blue (Food Grade Acetal POM-C)
- Ensinger TECAFORM® AH UD Blue (Ultra Detectable Acetal POM-C)
- Ensinger TECAFORM® AD HPV13 BROWN (Internal PTFE Lubricant POM-H)
- Rochling SUSTARIN® C MDT (Metal Detectable Acetal POM-C)
- Rochling SUSTARIN® C XDT (X-ray Detectable Acetal POM-C)
- Westlake POMALUX® (POM-C)
Material Overview
One of the best uses of plastics is for food applications. With all the different types of food grade plastics on the market, choosing the right one might be a bit of a challenge. If you’re looking for an all-around great material though, one of the best plastics for food grade applications is Delrin®.
It’s high mechanical strength, easy machinability, and good resistance to cleaning agents makes it useful in applications for deflectors, scrapers, needle blocks, object slides, cheese baskets, and throughfeed fillers in the food industry.
Properties of Delrin®
Delrin® is a crystalline plastic that has an excellent balance of both strength and resistance. It is a bridge between metals and plastics in the sense that it is both rigid and capable of holding its form because of its high creep resistance, and also has the moisture, hydrocarbon and solvent resistance of a good plastic.
Delrin® has a high tensile strength and stiffness. This makes it an excellent plastic for machining. It also means that it offers good protection for storage applications of delicate food items that can be damaged easily. Another property is the plastic’s excellent wear and abrasion properties that will keep it looking good after many uses.
Delrin® also offers low moisture absorption. This is critical for foods that must be kept moist or for food applications that are going to be stored in coolers, freezers or other highly moist environments.
FDA Certified
In order for plastics to be used for food or consumable storage, they must be FDA compliant. Not only is Delrin® certified for use by the FDA, it is also certified by the NSF and USDA, enabling it to be used in dairy applications as well. These certifications allow you to safely and legally use Delrin® in any food grade applications that you see fit.
Excellent Replacement for Metal
Delrin® offers strength that can be used in the food production industry. Food-safe stainless metals are traditionally used, but they can be very costly and, of course, heavy. Parts made of Delrin® in a production environment can be lighter, thinner and allow for shorter molding cycles. This can help you to not only reduce costs, but make production outages shorter should something break down.
Delrin® is rated for high load mechanical applications such as gears and conveyers. Since it can be machined to any desired application, you can use it to replace costly and heavy metal parts in your food production systems. The operating temperatures of -40 °C to 120 °C mean that it can be used in a wide range of applications depending on your needs.
Acetal (Delrin®) plastics offer the following advantages:
- High strength, rigidity and toughness
- Good impact strength, even at low temperatures
- Low moisture absorption (at saturation 0.8%)
- Outstanding wear resistance and sliding properties
- Excellent machinability
- Good creep resistance
- High dimensional stability
- Good resistance to hydrolysis (up to ~140 °F)
- Excellent resilience/recovery elasticity
Industry Suppliers and Trade Names
The suppliers we source Acetal (Delrin®) from are listed along with the trade names they use:
- Ensinger TECAFORM® AH (POM-C)
- Ensinger TECAFORM® AD (POM-H)
- Ensinger DELRIN® 100, 150, 500, 511, 527, and 570
- Quadrant ACETRON® (POM-C)
- Rochling SUSTARIN® C (Hostaform) (POM-C)
- Rochling SUSTARIN® H (Hostaform) (POM-H)
- Westlake POMALUX® (POM-C)
Other common trade names include: Hostaform®, Celcon®, POM™, and ZL® 900
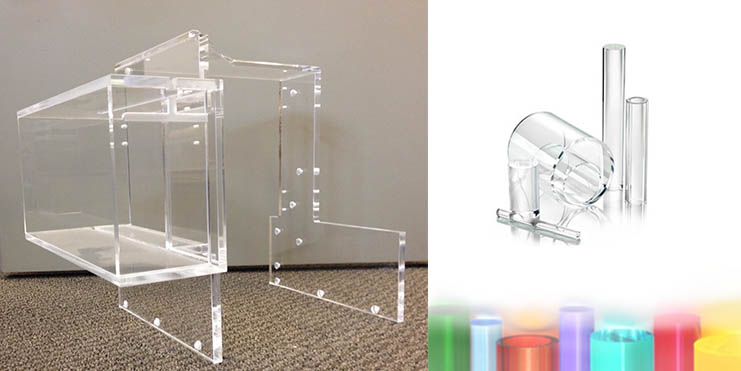
Acrylic (PMMA) Food Processing Plastics
Food Grade Acrylic (PMMA)
Below is a list highlighting specific Food Grade Acrylic (PMMA) we supply:
- Spartech Polycast™ Medical and Food Grade Sheet (Cast Acrylic) PMMA
- Plaskolite OPTIX (PMMA)
- EXCELON ACRYLIC® tubes
Material Overview
Acrylic or polymethyl methacrylate (PMMA) is a transparent plastic material with outstanding strength, stiffness, and optical clarity.
Quickly rising in popularity within the food and beverage industry, the use of optical plastics like Acrylic (PMMA) allow the use of advanced vision systems and old fashioned physical visual inspection for both sample analysis and continuous monitoring.
Optically clear components as well as multi-layer, Acrylic fluidic manifolds have seen tremendous growth in their adoption as a result of their flexibility and characteristics. Acrylic sheet is easy to fabricate, bonds well with adhesives and solvents, and is easy to thermoform.
Sample testing for contaminants, composition, purity and critical factors is a vital part of most industries in this area, including milk, other dairy, feed, oil and beverage production. This testing is often achieved using non-contact, light-based emission and receiving sensing technologies at various wavelengths. These all require a clear optical path directly to the substance, which can be achieved using clear plastic components.
Industry Suppliers and Trade Names
The suppliers we source Acrylic (PMMA) from are listed along with the trade names they use:
- Spartech Polycast™ Medical and Food Grade Sheet (Cast Acrylic) PMMA
- Plaskolite OPTIX (PMMA)
Other common trade names include: Plexiglas®, Altuglas®, Oroglas®, Solarkote®, ASTARIGLAS®, PALGLAS®, PMMA XT™
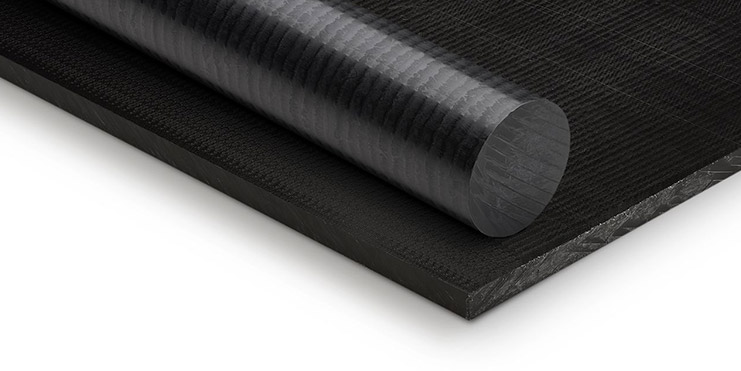
Acrylonitrile Butadiene Styrene (ABS) Food Processing Plastics
Material Overview
Acrylonitrile Butadiene Styrene material, commonly referred to as ABS plastic, is manufactured in standard stock shapes for machining, and is extruded in ABS plastic sheet and rod.
ABS polymer is an amorphous terpolymer which is manufactured by combining three different compounds. The three that make up ABS Plastic are acrylonitrile, butadiene and styrene plastic.
Using different combinations of these monomers, a wide range of different plastic ABS types can be manufactured to offer a wide spectrum of different ABS properties by means of branching or copolymerization. ABS is considered a food grade thermoplastic, and can be safe for use in food processing.
Industry Suppliers and Trade Names
The suppliers we source Acrylonitrile Butadiene Styrene (ABS) from are listed along with the trade names they use:
- Ensinger TECARAN™ ABS
- Rochling SUSTA ABS
- Westlake ABSYLUX®
Other common trade names include: PRIME-ABS® and ABS™
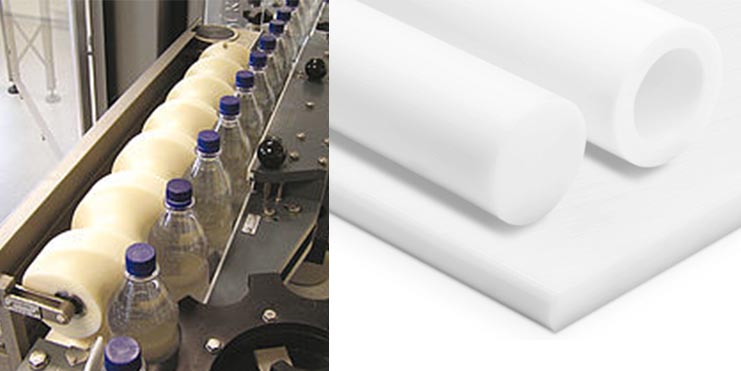
High Density Polyethylene (HDPE) Food Processing Plastics
Food Grade High Density Polyethylene (HDPE)
Below is a list highlighting specific Food Grade High Density Polyethylene (HDPE) we supply:
- EXCELON BEV-A-LINE® Tubing, EXCELON LLDPE, EXCELON LDPE, EXCELON HDPE, and EXCELON PE
- Rochling POLYSTONE® G Cut-Rite 51 (HDPE Cutting Board)
- SIMONA® HDPE Cutting Board and SIMONA® Low Friction PE
- Vycom Sanatec® HDPE and Sanatec® Lite HDPE
- Westlake Plastics ULTRA-ETHYLUX®
Material Overview
High Density Polyethylene (HDPE) is a thermoplastic polymer made from petroleum. As one of the most versatile plastic materials around, HDPE plastic is used in a wide variety of applications, including plastic bottles, milk jugs, shampoo bottles, cutting boards, and more.
Known for its outstanding tensile strength and large strength-to-density ratio, HDPE plastic has a high-impact resistance and melting point. Industrial-grade, FDA, NSF, and USDA-approved food-quality High Density Polyethylene (HDPE) boards are engineered to be low maintenance, safe and long lasting. Their textured surface provides a grip to hold food safely.
HDPE often replaces heavier materials which help companies and individuals alike pursue sustainable and affordable manufacturing and project goals. Thanks to its high malleability, rigid strength, and corrosion resistance. HDPE is the perfect combination of strength, cost-efficiency, and environmental friendliness.
Nonporous surfaces like plastic or glass are easier to clean than wood and thus better in terms of food safety. Wood is naturally porous, and those tiny fissures and grooves in wooden cutting boards can harbor bacteria which is why cutting boards made of wood aren’t allowed in commercial kitchens.
HDPE can be used in a variety of applications, making it especially useful for guiding pulleys, chain guidance, and suck and filter discs for the food industry.
Industry Suppliers and Trade Names
The suppliers we source High Density Polyethylene (HDPE) from are listed along with the trade names they use:
- Ensinger TECAFINE® HDPE
- Rochling POLYSTONE® G
- Simona America SIMONA® HDPE
- Vycom Corrtec® Hitec® + Sanatec®
- Westlake Plastics ULTRA ETHYLUX®
Other common trade names include: King ColorBoard® + King ColorCore® + King CuttingColors® + King StarBoard® + King MEDIGRADE® + King MicroShield® + King Plasti-Bal®, and DENSETEC® HDPE
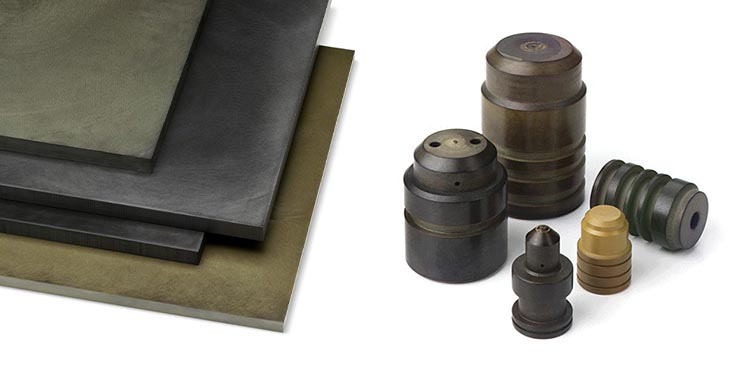
Polyamide-Imide (PAI) Food Processing Plastics
Material Overview
Polyamide-imides (PAI) are amorphous thermoplastic high performance polymers that are characterized among other things by high thermal stability, good chemical resistance and superior wear properties with temperature capabilities up to 275°C.
Parts manufactured from PAI plastic will exhibit high levels of tensile and compression strength that ensure good mechanical loading capability.
Additionally PAI material provides elevated levels of toughness and rigidity.
The mechanical rigidity coupled with low thermal expansion characteristics and thermal stability help to provide dimensionally stable finished components.
Other favorable PAI properties include high tensile and compressive strength.
Modifications of the PAI polymer are also possible with such materials as glass or carbon fibers, to increase strength and stiffness, or PTFE and other lubricants to reduce friction and increase bearing properties, even in dry running situations.
Users should find these material properties useful in the food processing industry as PAI can be a great alternative to larger metal parts that require strength and stiffness, and be used for a variety of applications in plant and machinery for meat, fish and poultry processing, dairy products, baked goods and confectionery production.
Industry Suppliers and Trade Names
The suppliers we source Polyamide-Imide (PAI) from are listed along with the trade names they use:
- Ensinger TECAPAI®
- Quadrant Torlon® (PAI)
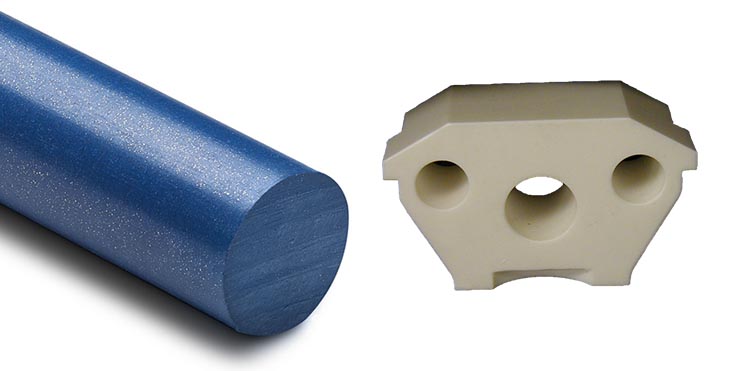
Polybutylene (PBT) Food Processing Plastics
Food Grade Polybutylene (PBT)
Below is a list highlighting specific Food Grade Polybutylene (PBT) we supply:
- Ensinger HYDEX® 4101 UD Blue (Ultra Detectable PBT)
- Ensinger HYDEX® 4101L (PBT Polyester Lubricated)
Material Overview
Polybutylene terephthalate, otherwise known as PBT plastic is a semi crystalline thermoplastic within the polyester family of polymers. Like other polyesters, PBT polymer is particularly suited for applications in the food industry because of its excellent resistance to chlorine and caustic cleaning solutions.
Food grade PBT can meet most agency requirements for food contact compliance, and is ideal for machined parts in food processing equipment. PBT’s resistance to many chemicals as well as its other properties makes it especially useful for applications with valve parts and pump housings.
PBT polyester material is also characterized by high strength, rigidity and thermal deformation resistance, as well as very high dimensional stability and a low tendency to creep. Furthermore, PBT polymers, like all polyesters, have very good friction and wear properties.
Compared to PET polyester, PBT has a better impact strength, particularly at low temperatures. Because of this characteristic, PBT is significantly easier to modify with fibers than PET, and is therefore also generally available as a fiber reinforced product.
In summary, polybutylene’s advantages include:
- High strength and rigidity
- Dimensionally stable
- Low tendency to creep
- Very good frictional and wear resistance
- Good impact strength
- Very low coefficient of thermal expansion
- Good chemical resistance to acids
- Excellent resistance to chlorine and caustics
- Very good electrical characteristics
- Very low moisture absorption
- Good adhesion and welding ability
Industry Suppliers and Trade Names
The suppliers we source Polybutylene (PBT) from are listed along with the trade names they use:
- Ensinger HYDEX® 4101 PBT
- Evonik VESTODUR®
- Rochling SUSTA® PBT
Other common trade names include: Arnite®
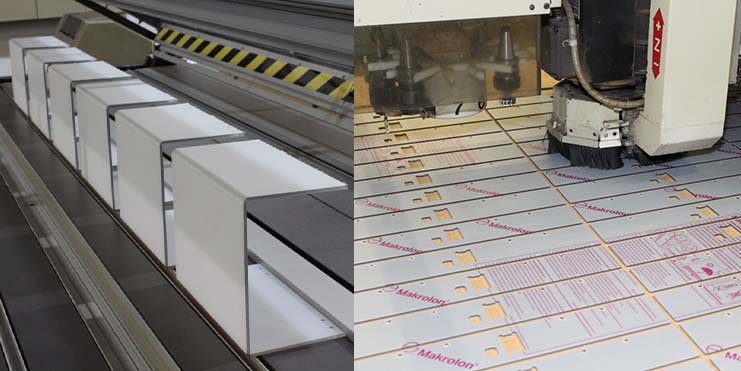
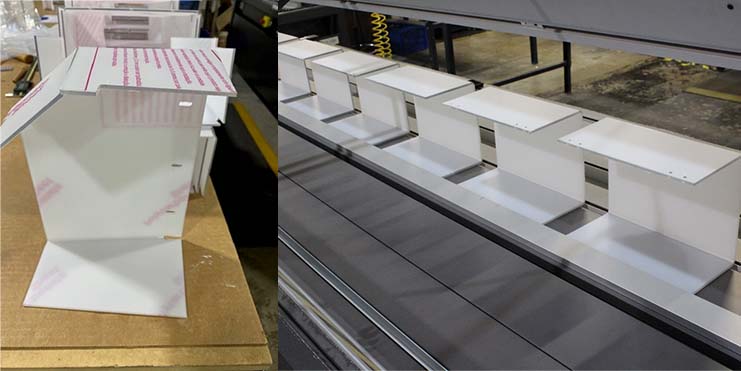
Polycarbonate (PC) Food Processing Plastics
Food Grade Polycarbonate (PC)
Below is a list highlighting specific Food Grade Polycarbonate (PC) we supply:
- Ensinger TECANAT® (PC)
- EXCELON® PC Tubing
- Plaskolite TUFFAK FD (Complies with Food and Drug Administration)
- SABIC LEXAN® (Food Grade Polycarbonate)
- Westlake Plastics ZELUX® GS (Gamma Stabilized PC)
Material Overview
Polycarbonate (PC) is a lightweight, amorphous thermoplastic with a unique combination of attributes that make it an ideal material for use in a wide variety of applications. Included are a number of home and kitchen applications involving direct contact with food and beverages that take advantage of polycarbonate’s inherent shatter-resistance, optical clarity, and heat-resistance.
Common examples include reusable 5-gallon water bottles, baby bottles, tableware such as plates and cups, and containers for storing food and reheating in a microwave oven.
Polycarbonate manufacturers tend to offer their polycarbonate material in the mid price range which makes it a very versatile material choice for a number of application uses.
Polycarbonate in the food processing industry is also used for structural and machine applications when clarity and impact strength are essential. This material has good insulating properties and is flame resistant.
In summary, polycarbonate’s advantages include:
- Low density
- Translucency (transparency for optical grades)
- Impact resistance
- Moderate chemical resistance (low solvent resistance)
- Good machinability
- Excellent dimensional stability
- Rigidity over a wide range of temperatures
Industry Suppliers and Trade Names
The suppliers we source Polycarbonate (PC) from are listed along with the trade names they use:
- Ensinger TECANAT® (PC)
- Plaskolite TUFFAK® (PC)
- Quadrant® PC 1000
- Rochling SUSTANAT®(PC)
- Spartech SunGard®
- Westlake Plastics ZELUX® (M, W) (PC)
Other common trade names include: PALGARD™ PC, PALSHIELD™ PC, PALSUN® PC, SUNLITE® PC, SunSky® PC, SUNTOP® PC, SUNTUF® PC, Rowlux® PC, RowTec® PC, EXCELON® PC, and PC™
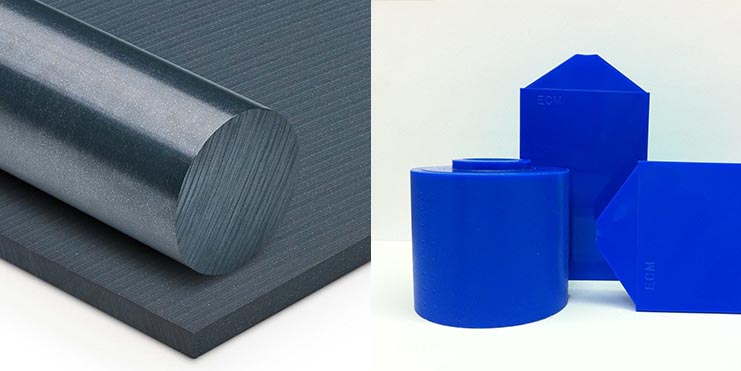
Polyetheretherketone (PEEK) Food Processing Plastics
Food Grade Polyetheretherketone (PEEK)
Below is a list highlighting specific Food Grade Polyetheretherketone (PEEK) we supply:
- Ensinger TECAPEEK® UD Blue (Ultra Detectable PEEK)
- Ensinger TECAPEEK® ID Blue (Metal Detectable PEEK)
- Ensinger TECAPEEK® MT, TECAPEEK® IM, and TECAPEEK® CM XP96
- Rochling SUSTAPEEK® XDT (X-ray Detectable PEEK)
Material Overview
Polyetheretherketone (PEEK) is a unique semi crystalline, engineering thermoplastic that offers excellent chemical compatibility, high dimensional stability and is easy to machine.
Lightweight, versatile plastics like PEEK have a proven track record stretching back over many decades in the processing and packaging of foods. Their success is based on a combination of material benefits which are brought to bear even at raised temperature levels. These include primarily good mechanical properties and high resistance to chemicals.
PEEK’s excellent mechanical properties and long-term performance over high temperatures makes it useful in applications for closing dies, filler nozzles, scrapers, valves, blenders, strippers, dosing systems, kneaders and mixing paddles in the food industry.
Parts manufactured from high temperature PEEK polymer can operate at temperatures up to 260°C (480°F) and have a melting point around 341°C (646°F).
PEEK food processing plastics can also come into direct contact with foodstuffs, for example in filling, mixing and portioning systems. Stringent demands are placed on these plastics, particularly in the case of plant components which come into direct contact with food. The main objective of EU and US regulations is to exclude any damaging effects due to the migration of substances.
For example, in the manufacture of cheese and dairy products, technical plastics are used in a number of different process steps, such as separating the whey and portioning, as well as transportation and cutting (for instance in SOS systems).
Detergents put high demands on plastics in terms of chemical resistance. Food grade PEEK fulfills these requirements and offers in addition high strength as well as excellent slide friction properties even at higher temperatures.
Furthermore, many food grade PEEK plastics are designed in an optically detectable blue color which leads to an increased process safety in foreign body control.
Industry Suppliers and Trade Names
The suppliers we source Polyetheretherketone (PEEK) from are listed along with the trade names they use:
- Ensinger TECAPEEK®
- Evonik VESTAKEEP® PEEK
- Quadrant KETRON®
- Rochling SUSTAPEEK
- Westlake Plastics AROLUX® PEEK
Other common trade names include: VICTREX® PEEK, Pyramid™ PEEK, Pyramid™ CC PEEK, and ZL®1500 PEEK
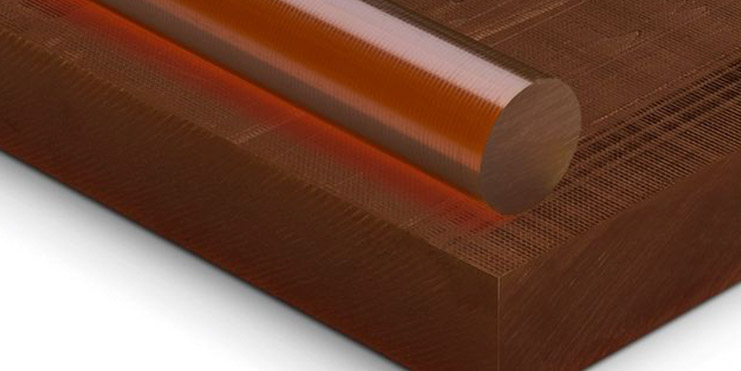
Polyetherimide (Ultem®) Food Processing Plastics
Food Grade Polyetherimide (Ultem®)
Below is a list highlighting specific Food Grade Polyetherimide (Ultem®) we supply:
Material Overview
Polyetherimide (PEI) material is an amorphous thermoplastic with high mechanical strength and rigidity. For this reason, it is widely used as a metal replacement material in many industries including food processing.
Unfilled PEI thermoplastic is translucent and amber in color with exceptional mechanical, thermal and electrical properties. PEI has long-term service temperatures up to 170 °C and good resistance to high-energy radiation.
In filled grades, the addition of glass fiber reinforcement provides users with a polyetherimide offering that has both greater tensile strength and rigidity, while also improving dimensional stability.
PEI Ultem® plastic has a remarkably high creep resistance over a wide temperature and a high permanent operating temperature. Furthermore, impressive resistance to hydrolysis, along with dimensional stability rounds out the portfolio of polyetherimide properties.
Ultem® is available in a wide range of colored stock shapes and can withstand sterilization techniques including ETO Gas, radiation, steam autoclaving, dry heat & cold sterilization.
Industry Suppliers and Trade Names
The suppliers we source Polyetherimide (PEI) from are listed along with the trade names they use:
Other common trade names include: SABIC Ultem™, LNP™ PEI, STAT-KON™ PEI, Ultem® PEI, Duratron PEI, and PEI™
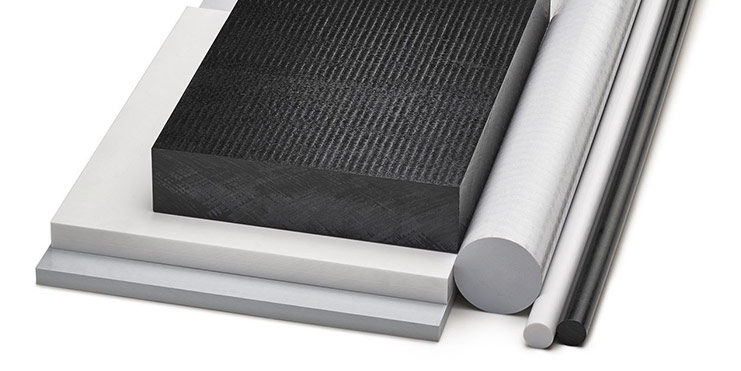
Polyethylene Terephthalate (PET) Food Processing Plastics
Material Overview
Polyethylene Terephthalate, also known as PET, is a clear, strong, and lightweight plastic that is widely used for packaging foods and beverages, especially convenience-sized soft drinks, juices and water. Virtually all single-serving and 2-liter bottles of carbonated soft drinks and water sold in the U.S. are made from PET.
PET was first synthesized in North America in the mid-1940s by DuPont chemists searching for new synthetic fibers. DuPont later branded its PET fiber as “Dacron.” Today, more than half of the world’s synthetic fiber is made from PET, which is called “polyester” when used for fiber or fabric applications.
PET is approved as safe for contact with foods and beverages by the FDA and health-safety agencies throughout the world. The safety of PET for food, beverage, pharmaceutical and medical applications has been repeatedly demonstrated through extensive studies, regulatory approvals, testing, and its widespread acceptance for more than 30 years.
Due to its good creep strength, low moisture absorption and outstanding dimensional stability, PET plastic material is extremely well suited for applications where complex parts and the highest requirements regarding dimensional accuracy and surface quality are needed. The thermal properties of PET support a good temperature stability as well as dimensional stability. All of the properties of PET make it a useful product in applications for spacer discs, guidance, slide bars, stop units, rollers and grabbers.
In summary, PET’s advantages include:
- High strength
- High rigidity and hardness
- Very low moisture absorption
- Good creep resistance
- Low sliding friction and sliding wear
- Resistant to hydrolysis (up to +70 °C)
- Not suitable for contact with media containing >50% alcohol
- Good chemical resistance against acids
- Good adhesion and welding ability
Industry Suppliers and Trade Names
The suppliers we source Polyethylene Terephthalate (PET) from are listed along with the trade names they use:
- Ensinger TECAPET®
- Quadrant ERTALYTE®
- Rochling SUSTADUR® PET
Other common trade names include: MECHETEC® PET, and ZL® 1400
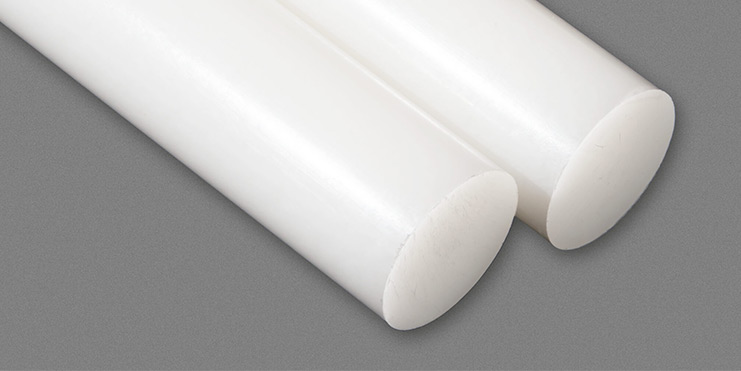
Polypropylene (PP) Food Processing Plastics
Food Grade Polypropylene (PP)
Below is a list highlighting specific Food Grade Polypropylene (PP) we supply:
- Ensinger TECAPRO MT + TECAFINE PP
- Rochling POLYSTONE® P
- Simona America SIMONA® PP
- Vycom Corrtec® Protec™ PP + Sanatec® PP
- Westlake Plastics PROPYLUX® DS (Food & Pharma Polypropylene)
- Westlake Plastics PROPYLUX® HS (Heat Stabilized Polypropylene)
- Westlake Plastics PROPYLUX® HS² (Heat Stabilized Polypropylene)
- Westlake Plastics PROPYLUX® VF (Void-Free Polypropylene)
Material Overview
Polypropylene is a semi crystalline thermoplastic manufactured by the catalytic polymerization of propene. Polypropylenes are universal standard plastics with well-balanced properties, providing excellent chemical resistance, high purity, low water absorption and good electrical insulating properties. PP material is also lightweight and weldable.
The strength and high melting point of polypropylene makes it the single-most used plastic packaging in the United States and United Kingdom.
PP material is somewhat stiff but less brittle than other plastics. It can be made translucent, opaque or a different color when it is manufactured. PP generally has a high melting point, making it particularly suitable for food packaging products that are used in microwaves or cleaned in dishwashers, for example.
PP material is commonly used in food packaging to make yogurt containers, maple syrup containers, cream cheese containers and sour cream containers, as well as prescription drug bottles. Polypropylene can also be used in applications for transport boxes for food and fittings in the food industry.
Industry Suppliers and Trade Names
The suppliers we source Polypropylene (PP) from are listed along with the trade names they use:
- Evonik Vestoran
- Quadrant PROTEUS® CO-POLYMER
- Spartech Polycast FormPro®
- Westlake Plastics PROPYLUX®
Other common trade names include: Inertec + DENSETEC®, and COR-X®
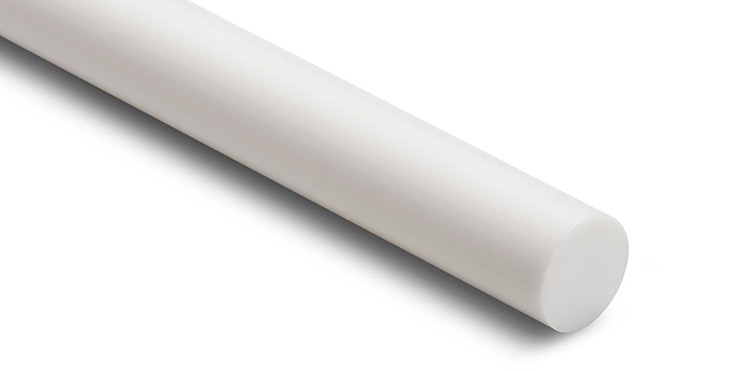
Polytetrafluoroethylene (Teflon®) Food Processing Plastics
Material Overview
Polytetrafluoroethylene (PTFE), colloquially referred to as Teflon®, is a semi crystalline fluoropolymer with many unique characteristics.
PTFE material is suitable for a wide variety of application possibilities in the processing and packaging of foods, due to its high chemical resistance and good mechanical properties. The attributes that PTFE plastic materials hold enhances the production speed and safety in food manufacturing.
These properties, along with the relevant food contact approvals, combine to provide an ideal solution for applications in bakery and food processing contact machinery.
PTFE has unusually high thermal stability and chemical resistance, as well as a high melting point that ranges from -200 to +260°C (-328 to +500°F) and can sustain short-term up to 300°C (572°F).
To improve its mechanical properties, PTFE plastics can be reinforced with additives such as glass fibre, carbon or bronze. In addition, PTFE products are self-lubricating with a low friction coefficient, excellent electrical resistance and a nonstick surface.
In summary, PTFE’s advantages include:
- Extremely high chemical resistance
- Very good temperature resistance (-200+260°C, short-term up to 300°C)
- Very low coefficient of friction
- Extremely low surface tension (practically no materials stick to PTFE, difficult to adhere to or weld)
- High coefficient of thermal expansion
- Relatively low strength/rigidity
- Low dielectric constant
- Flame resistance
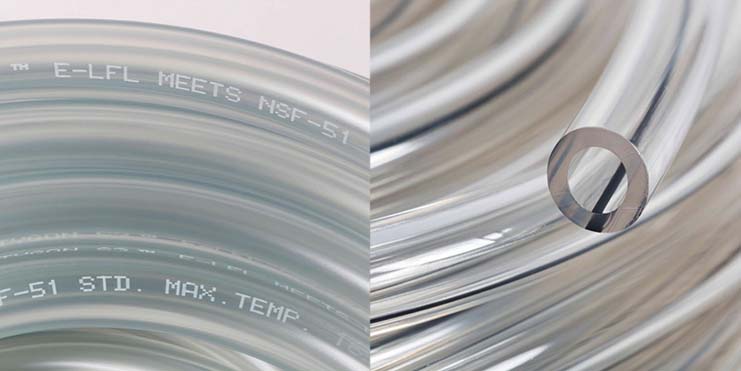
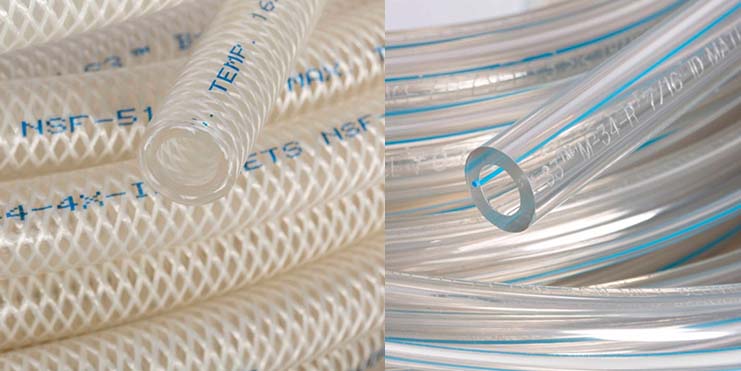
Polyvinyl Chloride (PVC) Food Processing Plastics
Food Grade Polyvinyl Chloride (PVC)
Below is a list highlighting specific Food Grade Polyvinyl Chloride (PVC) we supply:
- TYGON® PVC Tubing
- EXCELON PVC, EXCELON Flexible PVC Pipe, and EXCELON RNT Flexible PVC Tubing
Material Overview
Rigid PVC (polyvinyl chloride) is a strong, stiff, low cost plastic material that is easy to fabricate and easy to bond using adhesives or solvents. PVC tubing is used throughout the food industry. It can be found especially within dairy, milk, and beverage applications like filling line tubes.
The element chlorine is the primary ingredient used to make PVC and is biologically and chemically resistant. These two characteristics help PVC containers maintain the integrity of the products inside, including foods.
PVC is made into clear vinyl and used in blister packaging (packaging that has a plastic cavity or pocket) such as in packaging for breath mints or gum, for example.
In summary, PVC’s advantages include:
- Strong and stiff
- Low cost
- Easy to machine and fabricate
- Easy to thermoform
- Easy to weld using thermoplastic welding equipment
- Easy to join using solvents or adhesives
Industry Suppliers and Trade Names
The suppliers we source Polyvinyl Chloride (PVC) from are listed along with the trade names they use:
- Quadrant CORZAN® G2 SHEET
- Rochling Trovidur® (PVC-C, PVC-U, PVC-P)
- Simona America SIMONA® PVC
- TYGON® PVC
Other common trade names include: CLEARFLEX™ PVC, FLEX™ PVC, BraidFlex™ PVC, AG-TUF® PVC, Vincon™ PVC, EXCELON® PVC, and PVC™
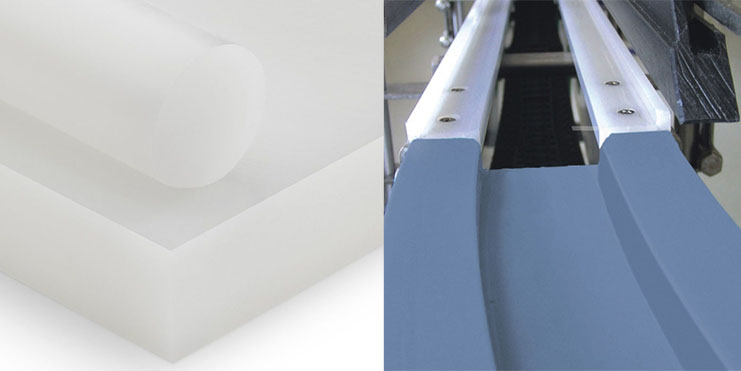
Ultra High Molecular Weight PE (UHMW) Food Processing Plastics
Food Grade Ultra High Molecular Weight PE (UHMW)
Below is a list highlighting specific Food Grade Ultra High Molecular Weight PE (UHMW) we supply:
- Rochling LubX® and LubX®C (UHMW-PE)
- Rochling Polystone® M MDT (Metal Detectable UHMW-PE)
- Rochling Polystone® M XDT (X-ray Detectable UHMW-PE)
Material Overview
Ultra High Molecular Weight PE (UHMW) is a tough, wear resistant plastic with a low coefficient of friction and outstanding impact strength. It’s non toxic, and doesn’t absorb moisture which is critical in baking and cooking environments. UHMW sheets meet FDA and USDA guidelines and are 3-A Dairy-approved. They’re also made for use at temperatures ranging from -250 C to 82 C.
In food service, materials need to be easy to sanitize, while keeping mold and bacteria at bay. Moreover, materials need to be able to stand up to potentially abrasive cleaners. UHMW is corrosion and chemical resistant enough to stand up to cleaners of all types. Best of all, it comes in several different finishes, meaning it’s easy to match a UHMW food shelf to any color scheme.
Its ability to withstand high temperatures, repeated stress and exposure to chemicals makes UHMW extremely ideal for conveyor systems. This plastic is also ideal for creating star wheels for conveyor systems, which help transport products through assembly and sorting lines quickly and efficiently.
In summary, Ultra High Molecular Weight Polyethylene’s advantages include:
- High impact resistance, even at low temperatures
- Good resistance to wear
- Minimal moisture absorption
- Excellent chemical resistance
- High corrosion resistance
- Non stick
- Very good electrical insulation
- High vibrational damping
- Pipeline for gas or drinking water
Industry Suppliers and Trade Names
The suppliers we source Ultra High Molecular Weight PE (UHMW) from are listed along with the trade names they use:
- Quadrant TIVAR® 1000
- Rochling Polystone® M (UHMW-PE)
- Westlake Plastics LENNITE™ (UHMW-PE)
Other common trade names include: Duravar®, Gar-Dur®, and POLYSLICK®
Have Any Questions?
Please contact David Alteri, our National Sales Manager for the Defense and Aerospace Division for more information on any of the products listed above or to get assistance on your next project:
office: 203.333.3128, Ext. 207
email: dalteri@modernplastics.com
Search Our Plastics Database
Learn more about our robust inventory of high performance plastics searchable by keyword, industry, manufacturer and shape.