High Performance Miltary Grade Plastics for the Defense and Aerospace Industry
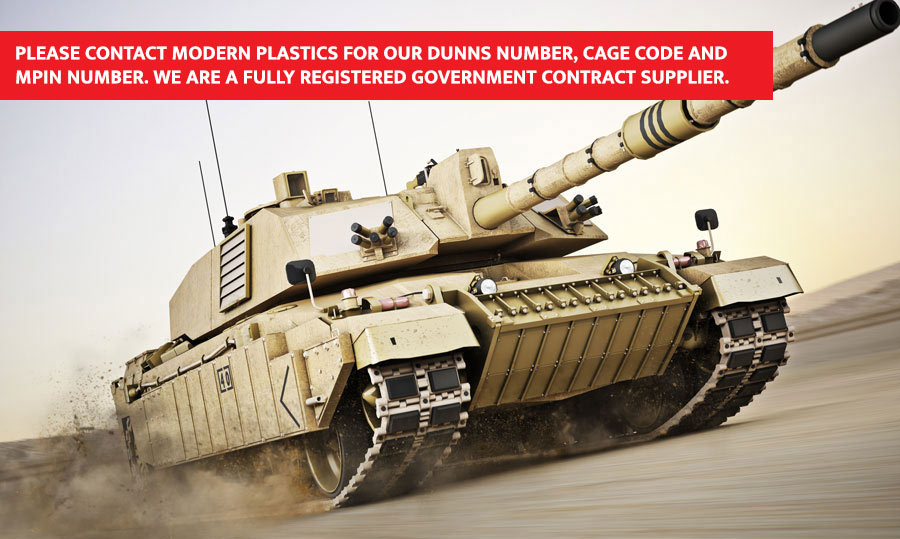
Engineering Plastics For Defense Industry
One of the largest distributors and fabricators of engineering plastics in the United States, Modern Plastics supply high performance engineering plastics to the defense and aerospace industry.
We have compiled this list to inform you of the various aircraft rated and military-grade engineering plastics we use to serve the defense and aerospace industry.
Engineering Plastics Supplier
If you have a question about any of the engineering plastics mentioned, our experts will be happy to assist you – contact us here or tap Interested in Our Services to email or text us at any time.
Why Trust Modern Plastics (Engineering Plastics Manufacturer)?
Modern Plastics has led by setting new industry standards throughout its 75 years in plastics distribution.
Modern Plastics is an ISO-Certified company (9001:2015 and AS9120B, 9001:2015 and AS9100D & 13485:2016) with a large inventory compliant to FAA, UL94, FAR 25.853, ASTM, DFAR’s, MIL-PRF-5425, MIL-PRF-8184, and MIL-PRF-25690 specifications.
Our knowledgeable Sales & Quality staff have over 25 years of experience servicing the defense and aerospace industry.
We inventory high performance engineering plastics that are lot controlled, individually line marked and bar-coded for complete material traceability.
Learn more about our services here.
Engineering Plastic Market
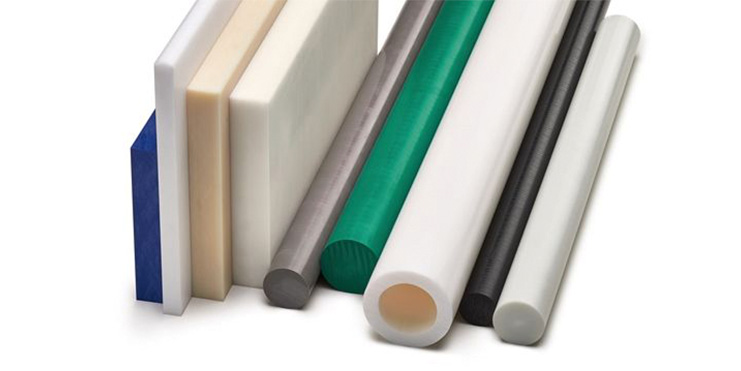
Acetal (POM)
Material Overview
POM material, commonly called Acetal (chemically known as Polyoxymethylene) is manufactured in standard stock shapes for machining and is extruded in sheets, rods and tubes.
POM plastic is a semi crystalline thermoplastic with high mechanical strength and rigidity.
Acetal polymer has good sliding characteristics and excellent wear resistance, as well as low moisture absorption.
The good dimensional stability and particularly good fatigue strength, as well as excellent machining ability, makes POM polymer a highly versatile engineering material, even for complex components.
POM-C can be used for a variety of aviation and space applications like airframe doors, aerospace fasteners, seal rings, main and nose landing gears, cabin seating, attenuation tubes, and antenna covers or bearing bushes for satellites.
POM-H can have very good slide friction properties and low water absorption making it useful in applications for slats and flaps on wings, actuation and control systems, and turbines and propeller systems.
POM plastics offer the following advantages:
- High strength, rigidity and toughness
- Good impact strength, even at low temperatures
- Low moisture absorption (at saturation 0.8%)
- Outstanding wear resistance and sliding properties
- Excellent machinability
- Good creep resistance
- High dimensional stability
- Good resistance to hydrolysis (up to ~140 °F)
- Excellent resilience/recovery elasticity
Industry Suppliers and Trade Names
The suppliers we source Acetal (POM) from are listed along with the trade names they use:
- Ensinger TECAFORM® AH (POM-C)
- Ensinger TECAFORM® AD (POM-H)
- Ensinger DELRIN® 100, 150, 500, 511, 527, and 570
- Quadrant ACETRON® and ERTACETAL® (POM-C)
- Rochling SUSTARIN® C (Hostaform) (POM-C)
- Rochling SUSTARIN® H (Hostaform) (POM-H)
- Westlake POMALUX® (POM-C)
Other common trade names include: Hostaform®, Celcon®, POM™, and ZL® 900
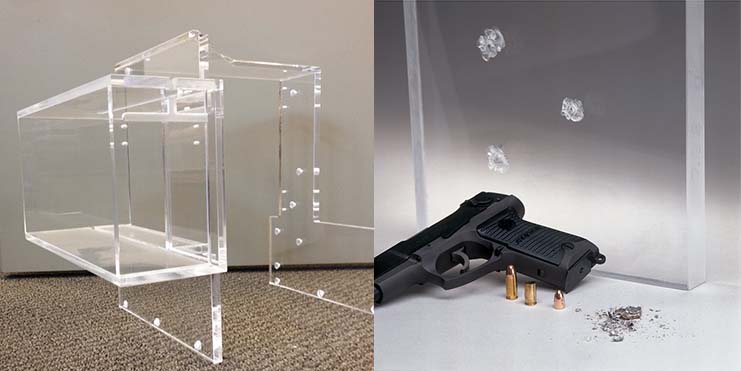
Acrylic (PMMA)
Material Overview
Acrylic or polymethyl methacrylate (PMMA) is a transparent plastic material with outstanding strength, stiffness, and optical clarity.
Acrylic sheet is easy to fabricate, bonds well with adhesives and solvents, and is easy to thermoform.
It has superior weathering properties compared to many other transparent plastics. Aerospace manufacturers use acrylic to meet the demands required in high performance environments.
The physical, chemical or optical properties in acrylic sheets can be modified in order to meet the requirements and specifications of militaries and aviation authorities.
Typical applications in aerospace and defense include cabin windows, fighter canopies, windscreens, wing-tip lenses, outer laminates and instrument panels for general aviation and military aircrafts.
Industry Suppliers and Trade Names
The supplier we source Acrylic (PMMA) from are listed along with the trade names they use:
- Plaskolite OPTIX (PMMA)
- Spartech Polycast™ Aerospace and Military Grade PMMA
Other common trade names include: Plexiglas®, Altuglas®, Oroglas®, Solarkote®, ASTARIGLAS®, PALGLAS®, PMMA XT™, and EXCELON ACRYLIC®
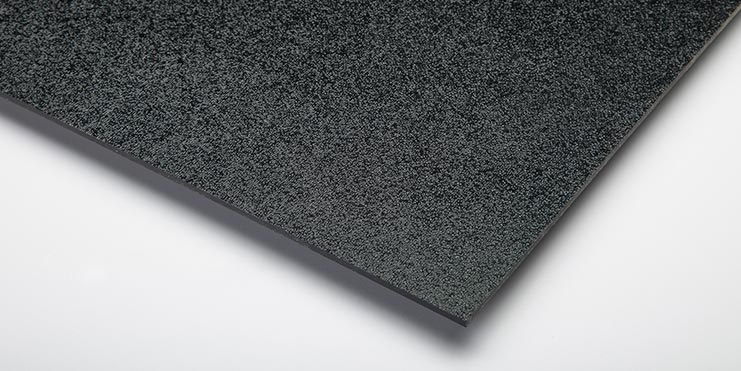
Acrylonitrile Butadiene Stryrene (ABS)
Material Overview
Acrylonitrile Butadiene Styrene material, commonly referred to as ABS plastic, is manufactured in standard stock shapes for machining, and is extruded in ABS plastic sheet and rod.
ABS polymer is an amorphous terpolymer which is manufactured by combining three different compounds. The three that make up ABS Plastic are acrylonitrile, butadiene and styrene plastic.
Using different combinations of these monomers, a wide range of different plastic ABS types can be manufactured to offer a wide spectrum of different ABS properties by means of branching or copolymerization.
ABS is flame and smoke-rated and a very lightweight material. This reduction in weight allows for reduced overall production costs for aircraft manufacturers and reduced operating costs and fuel consumption for aircraft operators.
ABS material occupies the unique position of being a bridge between the general industrial and other higher performance engineering thermoplastics.
Its performance is characterized by toughness and impact strength even at low temperatures, good stiffness and machinability. Because of this, ABS is incorporated into a wide range of aircraft interior solutions.
Industry Suppliers and Trade Names
The suppliers we source Acrylonitrile Butadiene Styrene (ABS) from are listed along with the trade names they use:
- Ensinger TECARAN™ ABS
- Rochling SUSTA ABS
- Spartech Royalite™ ABS
- Westlake ABSYLUX®
Other common trade names include: PRIME-ABS® and ABS™
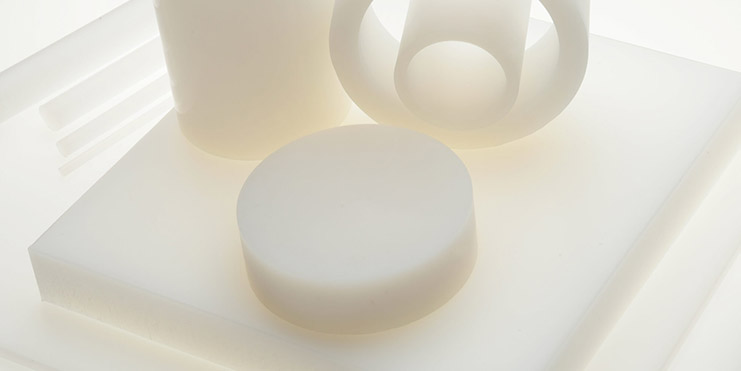
Fluorinated Ethylene Propylene (FEP)
Material Overview
FEP (fluorinated ethylene propylene) is a copolymer often used when chemical resistance, high purity, and low stiffness are required. FEP has outstanding electrical properties and UV resistance.
FEP is mainly used as electric wire insulation due to its dielectric properties and combustion resistance.
It has ultra-high extrusion speed and a wide processing window, which helps make it easy to process and use.
Because of these properties, this product performs very well as a primary insulation for plenum rated electrical data communication cables.
Additionally, it can be injection molded — particularly where the user needs very good flow to fill thin sections.
In summary, FEP’s advantages include:
- Ultra-high extrusion speed
- Exceptionally low dielectric constant and dielectric loss
- Wide processing window
- Extremely low flammability (high LOI)
- High thermal stability
- Very good weathering and UV stability
Common trade names include: Teflon™ and Versilon™
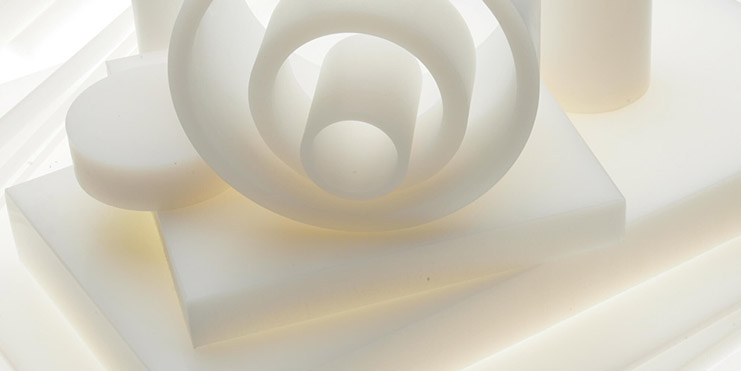
Perfluoroalkoxy Alkanes (PFA)
Material Overview
PFA (perfluoroalkoxy) is a tough, flexible fluoropolymer that is used for flexible tubing and fluid processing equipment when chemical resistance, high purity, and low stiffness are required.
PFA has outstanding electrical properties including high dielectric strength, a low dissipation factor, and a low dielectric constant.
The material has outstanding resistance to outdoor weathering.
In summary, PFA’s advantages include:
- Chemically inert to a wide variety of industrial chemicals and solvents
- Exceptional dielectric insulation properties
- Negligible moisture absorption
- Low coefficient of friction
- Non-stick surfaces
- Excellent weather resistance
Common trade names include: Teflon™ and Versilon™
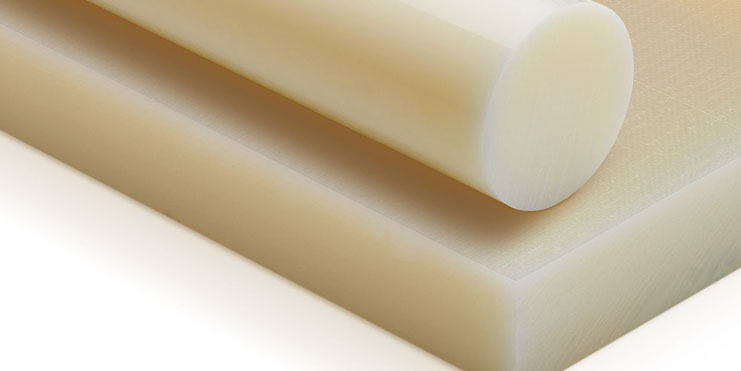
Polyamide (Nylon)
Material Overview
Nylon is a strong, stiff engineering plastic with outstanding bearing and wear properties frequently used to replace metal bearings and bushings often eliminating the need for external lubrication.
Other benefits include a reduction in part weight, less operating noise, and decreased wear on mating parts.
Nylons are typically described according to numbers (6, 66, 11, 12, etc.) which relate to their molecular structures. Although there are many types of Nylon, the two most common available in sheet, rod, and tube are Nylon 6 and Nylon 6/6.
Nylon 6 and Nylon 6/6– have very similar mechanical, thermal, and electrical properties. Both are available in a variety of colors and formulations that are engineered to meet specific application requirements.
Nylon 6– is generally manufactured into sheet, rod, and tube via a liquid casting process.
Casting is often the most cost effective method for producing large diameter rod, tube, and thick sheet. This process has the added advantage of allowing manufacturers to create custom near net (irregular) shapes.
Near net shapes are useful in the construction of parts that would yield poorly from standard sheet, rod, or tube stock.
Nylon 6/6– sheet, rod, and tube are usually produced by melting solid pellets of the polymer and processing them through a thermoplastic extruder.
Extrusion is a fast and economical method for making small diameter rod, tube, and thin sheet.
Unlike cast Nylon 6 stock shapes, extruded Nylon 6/6 sheet, rod, and tubing can be manufactured to any length, which can be an advantage for cost effectively yielding finished parts.
Nylon can be incorporated into a variety of aerospace and defense components, such as handles for support, gallery trolleys, external light covers, and tubing and piping. Using nylon can provide weight reduction, design flexibility, and a simplified assembly process.
In summary, Nylon’s advantages include:
- Excellent bearing and wear properties
- Strong and stiff
- Good chemical resistance
- Easy to machine
- Easy to fabricate
- Reduced noise, weight, and wear of mating parts
Industry Suppliers and Trade Names
The suppliers we source Polyamide (Nylon) from are listed along with the trade names they use:
- Ensinger TECAMID® + TECANAT® + TECAST® + HYDLAR® Z (PA)
- Evonik VESTAMID® + TROGAMID® + VESTOSINT® (PA)
- Quadrant ERTALON® + MC® + MONOCAST® + NYLASTEEL® + NYLATRON® (PA)
- Rochling SUSTAMID® (PA)
Other common trade names include: Nylatech®, PA™, Nylon, Nycast®, Nyloil®, ZL® 250 PA, and ZL® 1100 PA
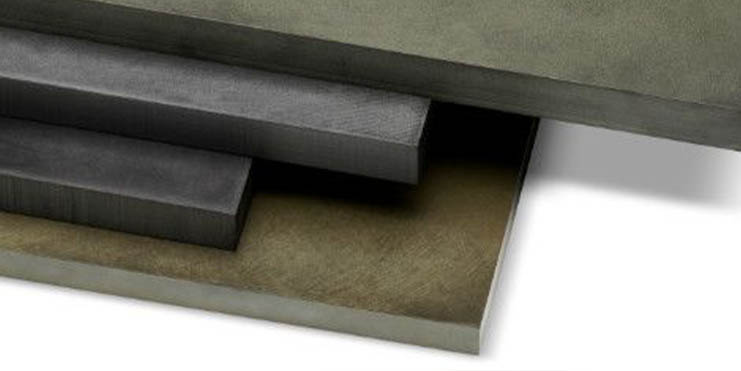
Polyamide-Imide (PAI)
Material Overview
Polyamide-imides (PAI) are amorphous thermoplastic high performance polymers that are characterized among other things by high thermal stability, good chemical resistance and superior wear properties with temperature capabilities up to 275°C.
Parts manufactured from PAI plastic will exhibit high levels of tensile and compression strength that ensure good mechanical loading capability.
Additionally PAI material provides elevated levels of toughness and rigidity.
The mechanical rigidity coupled with low thermal expansion characteristics and thermal stability help to provide dimensionally stable finished components.
Other favorable PAI properties include high tensile and compressive strength.
Modifications of the PAI polymer are also possible with such materials as glass or carbon fibers, to increase strength and stiffness, or PTFE and other lubricants to reduce friction and increase bearing properties, even in dry running situations.
Users should find these material properties useful in the aerospace industry as PAI can be a great alternative to larger metal parts that require strength and stiffness, and be used for fasteners, insulators, hydraulic valves, fan coverings, nacelles, and other aerospace components.
Industry Suppliers and Trade Names
The suppliers we source Polyamide-Imide (PAI) from are listed along with the trade names they use:
- Ensinger TECAPAI®
- Quadrant Torlon® (PAI)
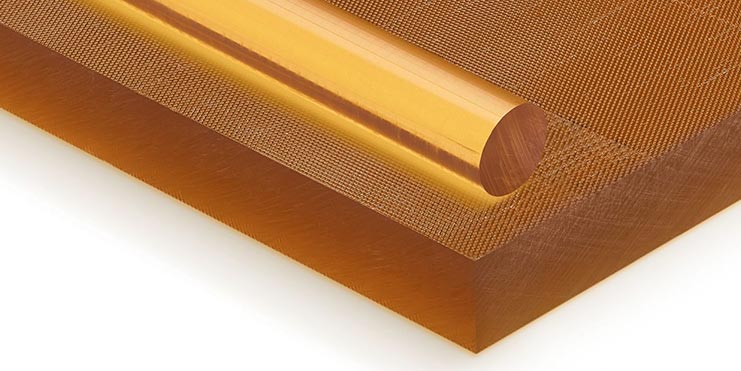
Polyarylsulfone (PSU)
Material Overview
Polyarylsulfones (PSU) belong to the group of polysulfones and are thermoplastic, transparent plastics.
Polysulfone (PSU) is a high temperature plastic with great mechanical strength and rigidity.
Apart from the high continuous use temperature, the outstanding characteristics of the material include good creep strength that is remarkably high over a wide range of temperatures.
PSU also has excellent dimensional stability, very good resistance to hydrolysis and good chemical compatibility. All of this makes PSU efficient in metal replacement and reducing weight for aerospace and defense components.
In summary, PSU plastic’s advantages include:
- High operating temperature (160°C)
- Very good resistance to hydrolysis (suitable for repetitive steam sterilisation)
- High toughness, even at low temperatures
- High dimensional stability
- Good electrical insulation
- High mechanical strength
- High rigidity
- High creep resistance over a wide range of temperatures
- Good radiation resistance
Industry Suppliers and Trade Names
The suppliers we source Polysulfone (PSU) from are listed along with the trade names they use:
- Ensinger TECASON® S (PSU)
- Quadrant® PSU 1000
- Rochling SUSTASON® (PSU)
- Westlake Plastics THERMALUX® (PSU)
Other common trade names include: PSU™ and Udel® PSU
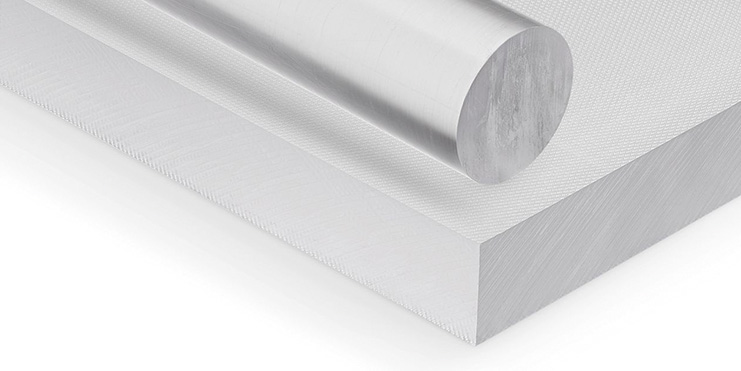
Polycarbonate (PC)
Material Overview
Polycarbonate plastic (PC) is manufactured in standard stock shapes for machining parts and is extruded in plate, sheet, rod and tube.
PC plastic is an amorphous thermoplastic with good electrical properties combined with superior impact strength and moderate chemical resistance.
Due to its low crystallinity and amorphous nature, PC has a high level of transparency.
Polycarbonate manufacturers tend to offer their polycarbonate material in the mid price range which makes it a very versatile material choice for a number of application uses.
Polycarbonate in aerospace and defense industries is often used for structural and machine applications when clarity and impact strength are essential. This material has good insulating properties and is flame resistant.
In summary, polycarbonate’s advantages include:
- Low density
- Translucency (transparancy for optical grades)
- Impact resistance
- Moderate chemical resistance (low solvent resistance)
- Good machinability
- Excellent dimensional stability
- Rigidity over a wide range of temperatures
Industry Suppliers and Trade Names
The suppliers we source Polycarbonate (PC) from are listed along with the trade names they use:
- Ensinger TECANAT® (PC)
- Plaskolite TUFFAK® (PC)
- Quadrant® PC 1000
- Rochling SUSTANAT®(PC)
- SABIC LEXAN® (Aircraft Grade Polycarbonate)
- SABIC LEXAN® (Mar-resistant Polycarbonate)
- Spartech SunGard®
- Westlake Plastics ZELUX® (M, W) (PC)
Other common trade names include: PALGARD™ PC, PALSHIELD™ PC, PALSUN® PC, SUNLITE® PC, SunSky® PC, SUNTOP® PC, SUNTUF® PC, Rowlux® PC, RowTec® PC, EXCELON® PC, and PC™
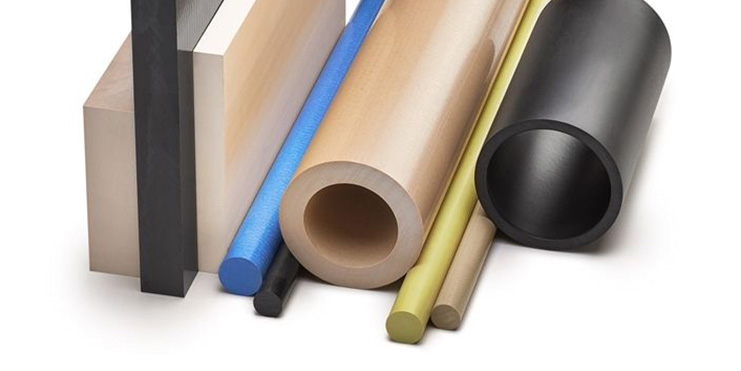
Polyetheretherketone (PEEK)
Material Overview
Polyetheretherketone (PEEK) is a unique semi crystalline, engineering thermoplastic that also offers excellent chemical compatibility, low susceptibility to stress cracking, clinically proven biocompatibility, high dimensional stability, good electrical insulation & it is easy to machine.
Parts manufactured from high temperature PEEK polymer can also operate at temperatures up to 260°C (480°F) and have a melting point around 341°C (646°F).
PEEK has excellent mechanical strength and impact properties.
It also has good dimensional stability and can be sterilized via steam autoclave, EtO gas and or conventional gamma radiation.
Experienced users have come to realize the added value that PEEK materials bring, by offering the possibility of manufacturing parts that are lighter, stronger and able to survive longer in harsh environments.
PEEK improves modulus retention at 290°C, making them suitable for replacing metal in components near the engine of planes.
Aileron, sensor plates, housing for fueling systems, fuselage, leading edge/J-nose, nacelle, and other aviation parts can be made from PEEK plastic.
Industry Suppliers and Trade Names
The suppliers we source Polyetheretherketone (PEEK) from are listed along with the trade names they use:
- Ensinger TECAPEEK® GF30 and PVX
- Evonik VESTAKEEP® PEEK
- Quadrant KETRON®
- Rochling SUSTAPEEK
- Westlake Plastics AROLUX® PEEK
Other common trade names include: VICTREX® PEEK, Pyramid™ PEEK, Pyramid™ CC PEEK, and ZL®1500 PEEK
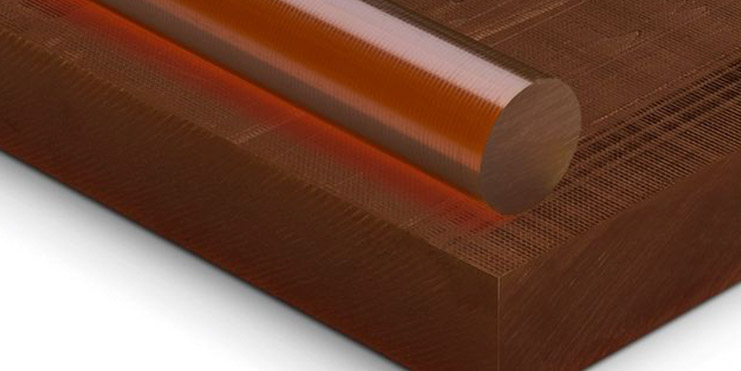
Polyetherimide (PEI) – Ultem®
Material Overview
Polyetherimide (PEI) material is an amorphous thermoplastic with high mechanical strength and rigidity.
Unfilled PEI thermoplastic is translucent and amber in color with exceptional mechanical, thermal and electrical properties.
In filled grades, the addition of glass fiber reinforcement provides users with a polyetherimide offering that has both greater tensile strength and rigidity, while also improving dimensional stability.
PEI Ultem® plastic has a remarkably high creep resistance over a wide temperature and a high permanent operating temperature.
Furthermore, impressive resistance to hydrolysis, along with dimensional stability rounds out the portfolio of polyetherimide properties.
Ultem® is available in a wide range of colored stock shapes and can withstand sterilization techniques including ETO Gas, radiation, steam autoclaving, dry heat & cold sterilization.
PEI has long-term service temperatures up to 170 °C and good resistance to high-energy radiation.
PEI can be made into components for antenna constructions, twin pulleys or output pulleys for baggage-tray lifts, and components for interior equipment in the aerospace industries.
Industry Suppliers and Trade Names
The suppliers we source Polyetherimide (PEI) from are listed along with the trade names they use:
Other common trade names include: SABIC Ultem™, LNP™ PEI, STAT-KON™ PEI, Ultem® PEI, Duratron PEI, and PEI™
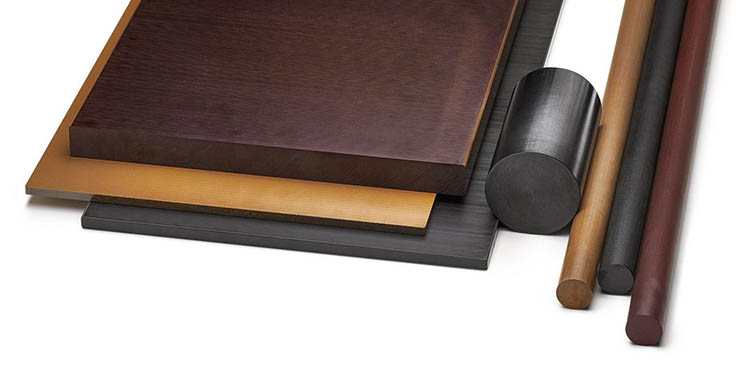
Polyimide (PI)
Material Overview
PI material, (chemically known as Polyimides) is manufactured in standard stock shapes for machining and is produced in sheet, rod and tube.
In addition to the sintering process used to produce stock shapes, finished components can be cost effectively produced in larger quantities using the direct forming process.
PI plastic is a non melting high temperature polymer. Strength, dimensional stability, and creep resistance remain high even at temperatures above 260°C.
Low wear rates combined with the ability to work under unlubricated conditions and high pV-rates makes it the ideal material for challenging friction and wear applications, extending lifetime and reducing maintenance costs.
Its high purity and low outgassing are needed for applications in the vacuum, aerospace and semiconductor industries.
In summary, Polyimide’s advantages include:
- Non melting high temperature polyimide
- Long term thermal stability 300°C (short term up to 400 °C)
- High heat resistance up to 470 °C (HDT/A)
- Good cryogenic properties down to -270 °C
- High strength, modulus and stiffness also at high temperatures over 260 °C
- Excellent thermal and electrical insulation
- High purity, low outgassing in vacuum conditions
- Good machinability
- Inherently flame retardant
Industry Suppliers and Trade Names
The suppliers we source Polyimide (PI) from are listed along with the trade names they use:
- Ensinger TECASINT® (PI)
- Quadrant DURATRON® (PI)
Other common trade names include: Pyramid™ PI
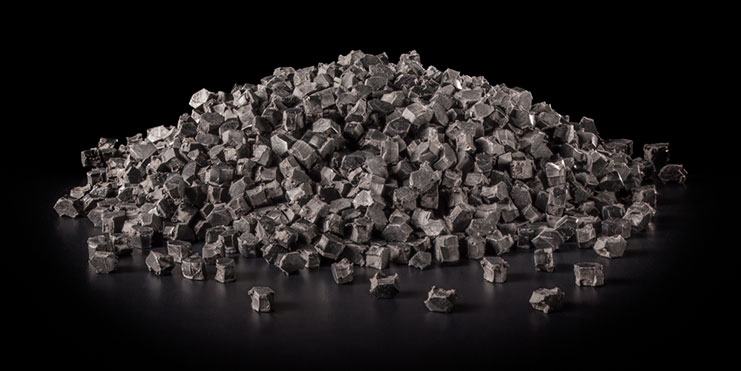
Polyphenylene Oxide (PPO) – Noryl®
Material Overview
Polyphenylene Oxide (PPO) Noryl® has outstanding mechanical, thermal and electrical properties. Very low moisture absorption and low thermal expansion make Noryl® one of the most dimensionally stable thermoplastics available.
Noryl® is widely used for electrical housings and structural components since it has excellent insulating properties, flame resistance, and dimensional stability over a wide range of service temperatures.
Noryl® is often selected for fluid handling applications since it has low moisture absorption and excellent strength and stiffness and is easily machined, fabricated, painted and glued.
In summary, Noryl® advantages include:
- Strong and stiff
- Good impact resistance
- Good dimensional stability
- Easy to machine
Industry Suppliers and Trade Names
The suppliers we source Polyphenylene Oxide (PPO) Noryl® from are listed along with the trade names they use:
Other common trade names include: PPO™
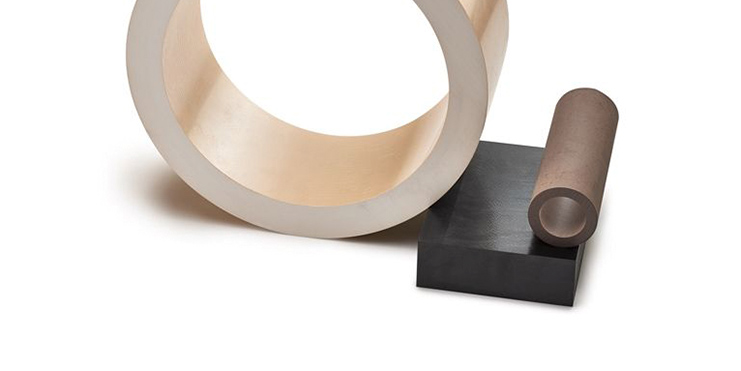
Polyphenylene Sulfide (PPS)
Material Overview
Polyphenylene Sulfide (PPS) plastic is a semi crystalline, high temperature thermoplastic polymer.
Due to its structure, PPS is a very chemically resistant polymer with amazing mechanical strength, even at temperatures above 200°C (392°F), very stable dimensionally with low susceptibility to creep.
In addition to its low water absorption, PPS polymer also has good dimensional stability and excellent electrical properties.
PPS can be incorporated into many aerospace and defense applications like doors and cable ducts, refueling and fueling systems, torque cylinders, pipe holders, and many other aerospace components.
In summary, PPS’s advantages include:
- High purity characteristics
- High crystallinity
- Good electrical insulation
- High mechanical strength
- Excellent high temperature resistance
- Very high chemical resistance
- Creep resistance
- Dimensional stability over wide variations of temperature and moisture levels
Industry Suppliers and Trade Names
The suppliers we source Polyphenylene Sulfide (PPS) from are listed along with the trade names they use:
- Ensinger TECATRON® GF40 (PPS)
- Quadrant TECHTRON® (PPS)
- Rochling SUSTATRON® (PPS)
- Solvay Ryton® (PPS)
- Westlake Plastics Arolux ™ (PPS)
Other common trade names include: Fortron® PPS, Pyramid™ PPS, and PPS™
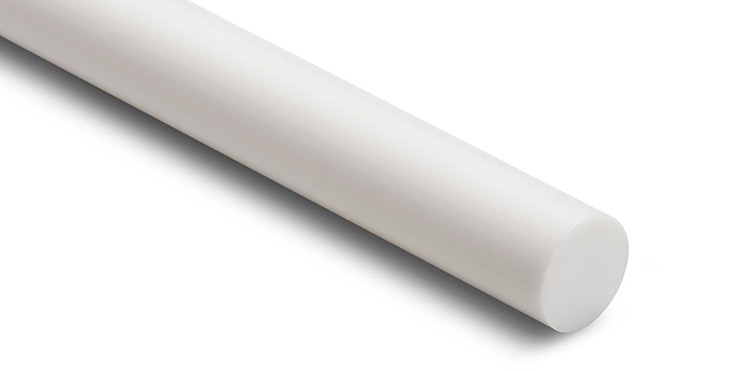
Polytetrafluoroethylene (PTFE) – Teflon®
Material Overview
Polytetrafluoroethylene (PTFE), colloquially referred to as Teflon®, is a semi crystalline fluoropolymer with many unique characteristics.
This fluoropolymer has unusually high thermal stability and chemical resistance, as well as a high melting point that ranges from -200 to +260°C (-328 to +500°F) and can sustain short-term up to 300°C (572°F).
In order to improve the mechanical properties, PTFE plastics can be reinforced with additives such as glass fibre, carbon or bronze.
In addition, PTFE products are self-lubricating with a low friction coefficient, excellent electrical resistance and a non stick surface.
Chemically resistant to fuels and with a low co-efficient of friction, filled grades of PTFE give greater resistance to wear and deformation under load.
PTFE can be made into a ball seat for in-flight re-fueling systems, torque cylinders, fixing elements, pipe holders, and other aerospace components.
In summary, PTFE’s advantages include:
- Extremely high chemical resistance
- Very good temperature resistance (-200+260°C, short-term up to 300°C)
- Very low coefficient of friction
- Extremely low surface tension (practically no materials stick to PTFE, difficult to adhere to or weld)
- High coefficient of thermal expansion
- Relatively low strength/rigidity
- Low dielectric constant
- Flame resistance
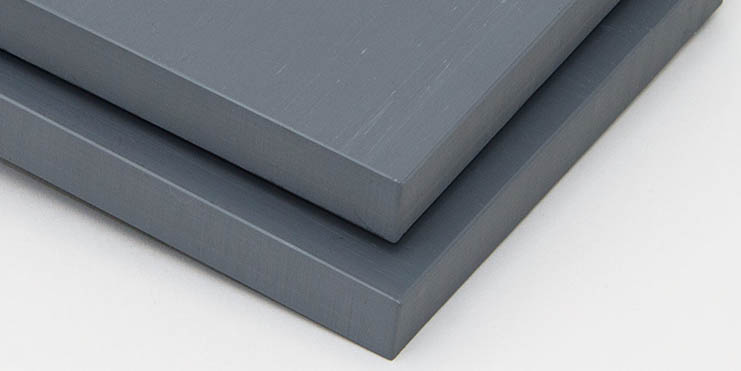
Polyvinyl Chloride (PVC)
Material Overview
Rigid PVC (polyvinyl chloride) is a strong, stiff, low cost plastic material that is easy to fabricate and easy to bond using adhesives or solvents.
PVC is also easy to weld using thermoplastic welding equipment. It is frequently used in the construction of tanks, valves, and piping systems.
FAA compliant for flame and heat resistant grades available, thus making PVC a great choice for aircraft interior components and for commercial, military, private aircraft, and helicopter manufacturers.
In summary, PVC’s advantages include:
- Strong and stiff
- Low cost
- Easy to machine and fabricate
- Easy to thermoform
- Easy to weld using thermoplastic welding equipment
- Easy to join using solvents or adhesives
Industry Suppliers and Trade Names
The suppliers we source Polyvinyl Chloride (PVC) from are listed along with the trade names they use:
- Quadrant CORZAN® G2 SHEET
- Rochling Trovidur® (PVC-C, PVC-U, PVC-P)
- Simona America SIMONA® PVC
- TYGON® PVC
- Vycom Celtec®, Corrtec®, Flametec®, Thermax®, and Seaboard® (PVC)
Other common trade names include: CLEARFLEX™ PVC, FLEX™ PVC, BraidFlex™ PVC, KömaCel PVC, KömaTex PVC, KömaDur PVC, AG-TUF® PVC, Duraclad® PVC, PALBOARD™ PVC, PALCLEAR® PVC PALIGHT® PVC, PALOPAQUE® PVC, PALRUF® PVC, Vincon™ PVC, EXCELON® PVC, and PVC™
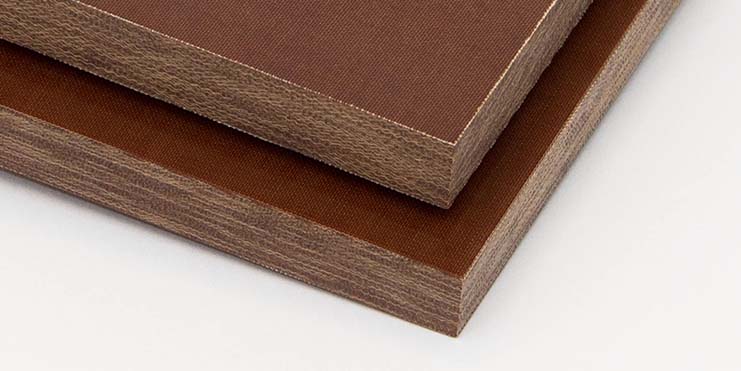
Thermoplastics Composites (Phenolic)
Material Overview
Phenolic Plastics or micarta plastics are a laminated plastic created by the impregnation of layers of a substrate with a resin then formed utilizing heat and pressure.
The resins are generally Phenolic, silicone, melamine or epoxies while the substrate materials range from paper and cotton to glass.
The resulting material is extremely versatile and used in a variety of applications. Also referred to as phenolic laminates, the notable properties of laminates include impressive resistance to shock, heat, stress, and corrosive chemicals.
Phenolic plastics are able to be machined, drilled, punched, sanded, tapped, turned, milled, sheared and cut.
The dielectric properties make this an excellent insulator which is used in applications from electrical transformers to circuit boards.
Common trade names include: ACCULAM®, Synthane®, Micarta®, and Garolite®
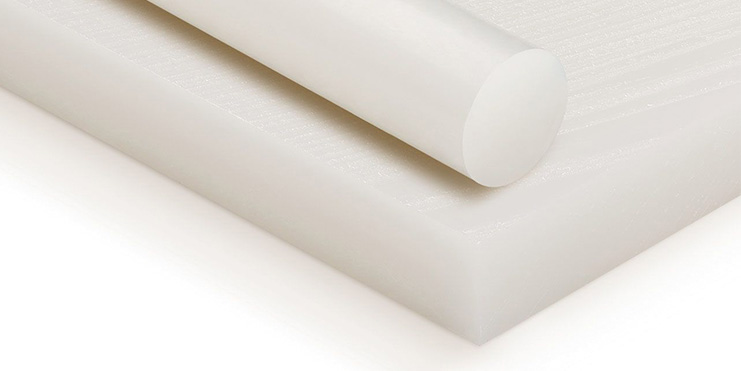
Polyvinylidene fluoride (PVDF) – Kynar®
Material Overview
Polyvinylidene fluoride (PVDF) is an opaque, semi crystalline, thermoplastic fluoropolymer.
PVDF is characterized by excellent chemical resistance without having the disadvantages of low mechanical values and/or processing difficulties which can be experienced with other fluoroplastics.
It is also inherently UV stable for good outdoor exposure, has great flame resistance (UL 94 V-O), and performs well in abrasion resistance tests making it suitable for many defense and aviation applications.
Industry Suppliers and Trade Names
The suppliers we source Polyvinylidene fluoride (PVDF) from are listed along with the trade names they use:
- Ensinger TECAFLON® PVDF
- Quadrant SYMALIT® PVDF
- Rochling POLYSTONE® PVDF and SUSTAPVDF
- Simona America SIMONA® PVDF
- Vycom Flametec® and Kytec® PVDF
- Westlake Plastics Kynar® 740 PVDF and Fluorolux™ PVDF
Other common trade names include: PVDF™
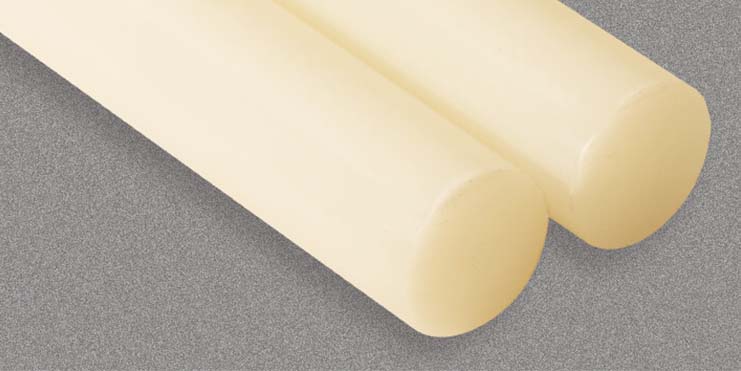
Ethylene Chlorotrifluoroethylene (ECTFE) – Halar®
Material Overview
Ethylene Chlorotrifluoroethylene (ECTFE), also known as Halar®, is a partially fluorinated semicrystalline polymer offering an array of mechanical properties and thermal and chemical resistance while also being easy to process.
Halar® has excellent corrosion and chemical resistance and performs well in many applications at temperatures up to 300° F.
It has excellent mechanical properties and extraordinary impact strength at temperatures ranging from -104° F to 302° F.
Halar® is extremely low in permeability from liquids, gases and vapors. It is resistant to most corrosive chemicals, except for hot amines and ketones.
The surface is very smooth and its purity is high. Halar® weathers well and is highly resistant to radiation.
Typical applications include semiconductor process equipment, chemical storage, fluid handling, solid and lined pipe, tanks and tank linings, pump and valve components, components for wet-process stations, and centrifuge parts.
Industry Suppliers and Trade Names
The suppliers we source Ethylene Chlorotrifluoroethylene (ECTFE) from are listed along with the trade names they use:
- SIMONA® ECTFE
- Westlake Plastics Halar® ECTFE
Other common trade names include: E-CTFE™
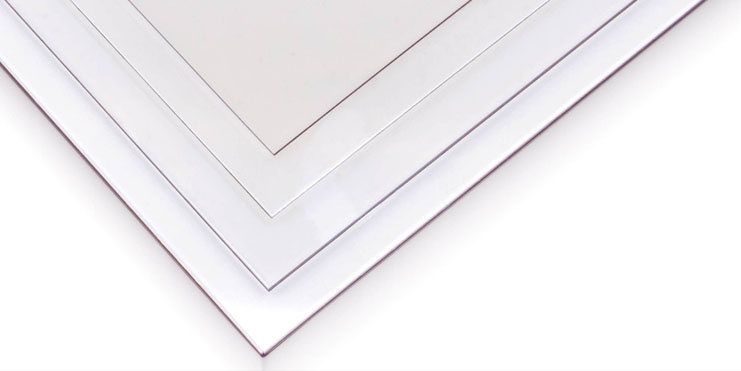
Polyethylene Terephthalate Glycol (PETG)
Material Overview
Polyethylene Terephthalate Glycol (PETG) is a transparent thermoplastic polyester that provides significant chemical resistance, durability, and excellent formability for manufacturing.
PETG can be easily vacuumed and pressure-formed as well as heat-bent thanks to its low forming temperatures.
This makes it exceptionally popular for consumer and commercial applications that involve 3D printing, or other heat-forming manufacturing techniques.
PETG is ideally suited for complex parts requiring fabrication, including deep thermoforming draws and precise molded-in details.
Additionally, PETG is well-suited for fabrication techniques like die cutting, routing, and bending.
In summary, PETG’s advantages include:
- Outstanding deep draw thermoforming
- Good impact resistance
- Chemical resistant
- Easy to fabricate and machine
- Good clarity
Industry Suppliers and Trade Names
The suppliers we source Polyethylene Terephthalate Glycol (PETG) from are listed along with the trade names they use:
Other common trade names include: Rowlux® and EXCELON® PETG
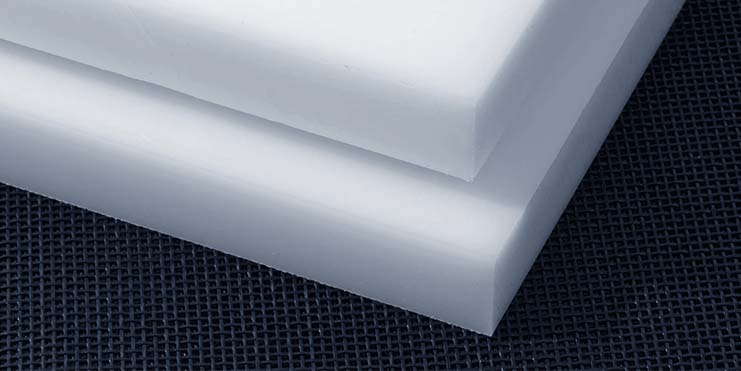
Polyethylene (PE)
Material Overview
Polyethylene (PE) is the most widely used thermoplastic polymer for fabricated parts and components.
It is available in a variety of grades and formulations to suit different needs. In general, polyethylenes offer excellent chemical and impact resistance, electrical properties and low coefficient of friction.
In addition, polyethylenes are lightweight, easily processed and offer near-zero moisture absorption.
In summary, polyethylene’s advantages include:
- Economical
- Low co-efficient of friction
- Excellent chemical resistance
- Stable in cryogenic environments
- Good impact resistance
Industry Suppliers and Trade Names
The suppliers we source Polyethylene (PE) from are listed along with the trade names they use:
- Ensinger TECAFINE® (HDPE)
- Quadrant TIVAR® (UHME-PE)
- Rochling Polystone® G (HDPE) and Polystone® M (UHMW-PE)
- Simona America SIMONA® Low Friction PE
- Vycom Corrtec®, Hitec®, Designboard®, Playboard®, Seaboard®, Sanatec® and TimberLine™
- Westlake ULTRA ETHYLUX® (HDPE), ETHYLUX® (LDPE), and Westlake Plastics LENNITE™ (UHMW-PE)
Other common trade names include: POLYFLEX™, King Cuttingboard®, King PipeGrade®, King Plasti-Shield®, EXCELON Bev-A-Line®, EXCELON® PE, Duravar®, GUR®, Gar-Dur®, GEHR UHMWPE™, POLYSLICK®, GEHR HDPE™, and DENSETEC® HDPE
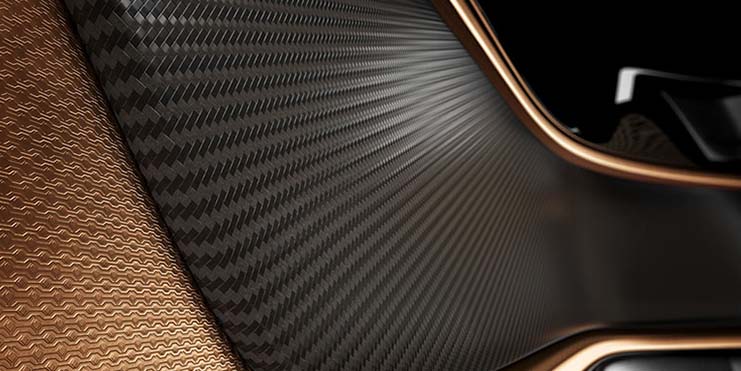
PVC/Acrylic Alloy (PVC-PMMA)
Material Overview
Extremely durable PVC acrylic alloys can be extruded in a range of colors, patterns, textures, thicknesses, and grades to optimize long-term performance, appearance, and cost effectiveness across demanding and diverse end-use applications.
Specialized grades are offered to satisfy requirements specific to thermoforming, membrane pressing, post-forming, brake-forming, and laminating-and to fit a broad range of specialized applications, ranging from medical equipment housings and aircraft tray tables to retail store fixtures and trade show displays.
Depending on grade, PVC acrylic alloys offer notched Izod Impact resistance up to 18 ft. lbs./in. (953 J/m), and are available in thicknesses from .028 to .500 inch (0.71mm to 12.7mm) to withstand levels of abuse from moderate to extreme.
Due to its high degree of toughness and resilience, some PVC acrylic alloys can also be stretched at room temperature to twice their original dimension without breaking.
Aviation applications include seat backs and seat components, sidewall panels and partitions, monuments and lavatory surfaces.
Industry Suppliers and Trade Names
The suppliers we source PVC acrylic alloys from are listed along with the trade names they use:
- SEKISUI Polymer Innovations Kydex®
- Simona America Boltaron®
Have Any Questions?
Please contact David Alteri, our National Sales Manager for the Defense and Aerospace Division for more information on any of the products listed above or to get assistance on your next project:
office: 203.333.3128, Ext. 207
email: dalteri@modernplastics.com
Search Our Plastics Database
Learn more about our robust inventory of high performance plastics searchable by keyword, industry, manufacturer and shape.